Cómo soldar componentes electrónicos
Autor:
Monica Porter
Fecha De Creación:
21 Marcha 2021
Fecha De Actualización:
1 Mes De Julio 2024
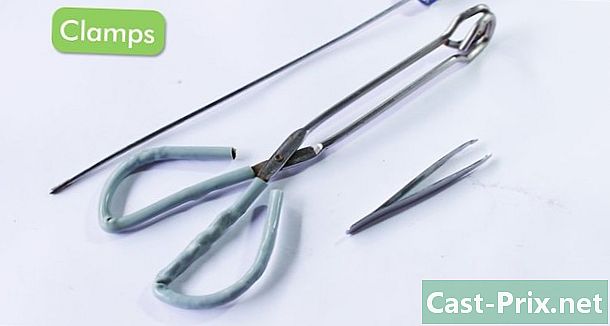
Contenido
En este artículo: Obtenga el equipo necesario Sujete los componentes Soldadura de pozo
Cualquier profesional aficionado o electrónico debe aprender a soldar componentes en agujeros de PCB. Puede obtener información sobre el equipo y las habilidades que necesita para saber cómo soldar componentes electrónicos correctamente.
etapas
Parte 1 Obtenga el equipo necesario
- Use un soldador con control de calor adecuado. Para soldar componentes electrónicos en una placa de circuito impreso, las mejores planchas de soldadura son potentes planchas de control de temperatura que evitan la descarga electrostática. Le permitirán soldar durante horas y son adecuados para proyectos más complejos. Para proyectos más simples, un soldador básico funcionará muy bien.
- Use un soldador fijo de 25 vatios para proyectos pequeños y 100 vatios para proyectos más grandes que contengan más cables.
- Si es posible, busque un soldador de temperatura variable, ya que esto le ayuda a evitar dañar la placa de circuito. Puede controlar la temperatura de la punta del soldador para ajustarse al trabajo a realizar.
-
Use un alambre de aleación adecuado. La aleación más utilizada en electrónica consiste en 60% de estaño y 40% de plomo, a veces señalado como 60/40. Se recomienda esta aleación si es nuevo en la soldadura, incluso si puede ser un poco peligroso y requiere una buena ventilación de la habitación, un medio de protección respiratoria y un soldador con una bomba.- Las aleaciones que no contienen plomo se están volviendo cada vez más populares. Requieren temperaturas de soldadura más altas y no se licúan tan bien como las aleaciones con plomo. Sin embargo, son más seguros y pueden ser más efectivos. La aleación base de 96.5% de estaño y 3.5% de plomo es la más eficiente y producirá una soldadura que ofrecerá menos resistencia a la corriente que cualquier otra aleación a base de estaño.
- Puede comprar aleaciones con o sin plomo en Internet o en tiendas especializadas.
-
Si es posible, intente encontrar hilo que contenga un fluidizador. El fluidizador es un aditivo que se encuentra en la aleación y que facilita la soldadura al eliminar y prevenir la oxidación al tiempo que mejora la fluidez de la aleación. Hay diferentes tipos- La colofonia generalmente es utilizada por aficionados. Después de soldar, deja un residuo marrón y pegajoso que no es corrosivo ni conductor, pero que puede limpiar con lisopropanol si lo desea. Hay diferentes grados de colofonia, el que más se usa es la "colofonia ligeramente activada".
- Estos diluyentes dejan un residuo transparente después de la soldadura que no es corrosivo ni conductor. El plastificante está diseñado para dejarse en la soldadura y en las áreas circundantes.
- Los plastificantes solubles en agua generalmente tienen una tasa de actividad más alta y dejan un residuo que se puede limpiar con agua. Este residuo es corrosivo y podría dañar la placa de circuito o los componentes si no lo limpia inmediatamente después.
-
Obtenga las placas de circuitos y componentes necesarios. En la mayoría de los casos, las soldaduras electrónicas solo se refieren a componentes que entran en agujeros en los circuitos impresos. Los componentes electrónicos tienen pestañas para pasar a través del orificio del circuito impreso antes de soldarlos al anillo de metal alrededor del orificio. El agujero puede ser chapado o no.- Existen técnicas ligeramente diferentes para soldar otros elementos, como cables, pero los principios del uso del soldador y el alambre de soldadura son los mismos.
-
Obtenga un clip para sujetar los componentes. Los componentes electrónicos generalmente son pequeños y necesitará pinzas o pinzas para mantenerlos en su lugar mientras usa el soldador y maneja la soldadura. Puede ser un poco complejo.- En general, una pinza tipo cocodrilo es la mejor solución para mantener los elementos en su lugar mientras los suelda.
Parte 2 Suelde los componentes
-
Prepare los componentes a soldar. Elija el componente correcto comprobando cuidadosamente su tipo y valor. Si está soldando resistencias, verifique su código de color. Doblar las piernas si es necesario teniendo cuidado de no romper el componente o doblar las piernas para que entren en el circuito. -
Tenga mucho cuidado y suelde los componentes en el lugar adecuado. Siempre debe soldar en un lugar bien ventilado, protegiéndose la nariz, la boca y los ojos. Asegúrese de dejar la plancha encendida cuando esté encendida, incluso cuando no la esté usando. Los soldadores pueden iniciar incendios fácilmente al prender fuego a su banco de trabajo.- Tienes que dejar unos veinte centímetros de espacio entre tu cara y los componentes electrónicos o podrían saltar en tu cara. La soldadura también podría salpicar.
-
Prepara el soldador. Derrita una pequeña cantidad de estaño al final del soldador. Este paso mejora la conducción del calor del hierro a la placa, lo que lo protege del calor.- Presione con cuidado el extremo del soldador (que tiene una pequeña cantidad de estaño). La punta del soldador debe tocar el orificio y el anillo.
- El extremo de la plancha no debe tocar el resto de las partes no metálicas de la placa de circuito impreso o la fibra de vidrio que puedan estar a su alrededor. Estas áreas podrían dañarse si aplicas demasiado calor.
-
Aplique el soldador en la superficie entre el orificio y el anillo. El fluidizador en el alambre de soldadura solo está activo durante un máximo de un segundo después de ser depositado en el punto de soldadura porque el calor lo consume lentamente. El orificio y el anillo deben estar lo suficientemente calientes como para que el cable de soldadura se derrita, no el punto de conexión. La aleación debe adherirse al anillo y al orificio gracias a su tensión superficial. A menudo se dice que el componente está "húmedo".- Si el alambre de soldadura no se derrite en el área, probablemente se deba al hecho de que no lo lava lo suficiente o que la superficie necesita ser limpiada de cualquier grasa o suciedad que pueda estar presente.
-
Deje de agregar aleación tan pronto como se llene el orificio. Como regla general, no debe necesitar más de una o dos gotas de aleación para cada orificio, aunque esto variará según los componentes. La cantidad indicada de aleación estará determinada por varios factores.- En los circuitos impresos revestidos, debe dejar de colocar la aleación una vez que pueda ver una red metálica cóncava alrededor del terminal del componente.
- En los PCB no chapados, debe dejar de colocar la aleación tan pronto como vea que se forma una rosca plana.
- Una cantidad excesiva de aleación podría formar una burbuja con una forma convexa, mientras que una cantidad demasiado pequeña formará una junta cóncava.
Parte 3 Soldadura de pozo
-
Actúa rápido. Desafortunadamente, es bastante fácil dañar un componente o placa si los calienta demasiado. Sin embargo, en la mayoría de los casos, puede proteger la placa y el componente actuando rápidamente. Mantenga un dedo en la placa de circuito cerca del punto de soldadura para asegurarse de que no se sobrecaliente.- Intente utilizar soldadores un poco menos potentes de lo que cree que necesita. Use un soldador de 30 vatios y practique soldar rápidamente para evitar aplicar demasiado calor.
- Si está trabajando en ambos lados de una placa de circuito, verifique que ambos lados estén limpios. Una buena soldadura se verá brillante y tomará la forma de un cono. Si parece "frío" y pálido, te lo has perdido.
-
Considere usar un radiador para componentes más sensibles. Algunos componentes (por ejemplo, diodos, transistores, etc.) son más susceptibles al daño por calor y requieren un pequeño disipador de calor de aluminio conectado a sus patas en el lado opuesto de la placa. Puede comprar estos pequeños radiadores de aluminio en la mayoría de las tiendas de electrónica. -
Aprenda a reconocer soldaduras donde haya suficiente aleación. Después de una buena aplicación del alambre de soldadura, la soldadura debe ser brillante y no pálida. Observe la soldadura para ver si se lava bien. Debe haberse derretido y fusionado con la superficie del componente electrónico en lugar de cubrirlo. De esta manera, cuando la soldadura se enfríe, formará una aleación con la superficie del metal.- La soldadura debe cubrir la superficie del componente de manera uniforme, no tanto como una bola, sino lo suficiente como para cubrir toda la superficie.
-
Mantenga limpio su soldador. Podría tener el hierro fluidificante, la colofonia en el alambre o pedazos de plástico quemándose en el hierro. Estos contaminantes evitan la formación de una aleación limpia entre los componentes electrónicos. Esto no es lo que desea porque aumenta la resistencia eléctrica y reduce la resistencia mecánica de la soldadura. Una pieza limpia de soldador es brillante en toda su superficie, sin residuos quemados.- Limpie el soldador entre cada soldadura que haga. Use una esponja húmeda o lana de hierro para limpiarlo a fondo.
-
Asegúrese de dejar que el soldador se enfríe por completo antes de mover los componentes. Deje enfriar solo durante cinco a diez segundos.Si los componentes están demasiado calientes para manipularlos, use alicates de punta plana o pinzas de cocodrilo unidas a un soporte con bisagras. Si lo observa con cuidado, la soldadura debería enfriarse justo delante de sus ojos. -
Entrena con componentes de recuperación. Es importante entrenar con componentes que de otro modo habría desechado antes de que desee soldar algo más importante. Recoja componentes viejos de una radio vieja o un buen dispositivo electrónico para que la basura los tenga en sus manos.- Nadie es perfecto, ni siquiera los profesionales. No se sienta mal si tiene que repetir una soldadura varias veces. Esto le ahorrará problemas que le harán perder el tiempo más tarde.
- La punta del soldador tiende a bloquearse con el tiempo (si la usa con frecuencia) debido a la acumulación de óxidos que se produce entre la punta de cobre y el mango de hierro. Las puntas chapadas generalmente no tienen este tipo de problema. ¡Si no quita la punta de cobre de vez en cuando, permanecerá atascada permanentemente en el soldador! Entonces es bueno para la basura. Cada 20 a 50 horas de uso, cuando hace frío, debe quitar la punta y rotarla de un lado a otro en redondo para que el residuo oxidado caiga, antes de volver a colocarla en su lugar. Ahora puede conservar su soldador durante muchos años.
- La mayoría de los soldadores tienen una punta que puede quitar. Estos consejos tienen una vida limitada y hay todas las formas y tamaños para acomodar muchos tipos de trabajo.
- Mantenga una pera o desoldador (que absorberá el metal fundido) o una trenza desoldadora (alambre de cobre fino que absorbe la soldadura fundida) cerca de la mano si la soldadura se desborda, si necesita desoldar un componente o si Debe eliminar el exceso de soldadura.
- El alambre de soldar, especialmente el alambre a base de plomo, contiene elementos peligrosos. Lávese las manos después de soldar y tenga cuidado ya que los objetos que contienen alambre de soldadura deben tirarse con el resto de los objetos peligrosos.
- Los soldadores son muy calientes. No ponga la punta en contacto con su piel. También debe usar siempre un soporte adecuado para mantener la punta de la plancha en el aire sobre su superficie de trabajo.